We were approached by a Czech manufacturer of die-cutting sheets with a request for a laser suitable for hardening the cutting edges of die-cutting sheets. Part of the specification was the exact definition of the hardening temperature, the size of the working area and the minimum required speed of work. As the customer is very experienced with laser hardening of its tools, all requirements were very clear and specific and were directed towards a single goal - to obtain a powerful and robust laser hardening solution with maximum production quality after integration of the laser subsystem into the production line.
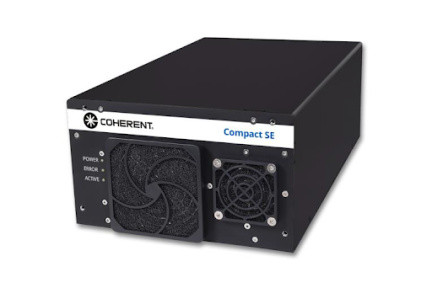
Testing
The principle of laser hardening is the rapid heating of the material to the hardening temperature, and any deviation from this temperature leads to the degradation of the entire already finished die-cut sheet. At the same time, a constant width of the laser track over the entire working area of the machine and many other requirements must be maintained. For this reason, we have chosen the following laser configuration for the job:
Laser source
|
Diode laser Coherent Compact SE
|
Process head
|
PHF50 with inline camera and pyrometer
|
Focal distance
|
f = 100 mm
|
Fiber diameter
|
200 µm
|
Working point size
|
0.3 mm
|
Coherent Compact SE diode laser
The air-cooled Coherent Compact SE diode laser is part of the complete Coherent Compact diode laser series. The maximum laser power is 100 W and the wavelength is 980 nm. The laser source is air-cooled, making it easy to integrate into production lines, and its design also allows it to be used as a stand-alone module or mounted in a 19" rack.
PHF50 process head
The lightweight, modular Coherent PHF50 process head is designed for low power laser systems. Its advantage is the availability of a large number of expansion modules such as pyrometer, inline camera, or lenses with different optical parameters.
The laser in the Coherent application lab is equipped with a process head that moves in the Z-axis, while the X- and Y-axis motion is provided by the movement of the workbench.The entire hardening process was monitored by an inline camera. The achievement and maintenance of the quench temperature was controlled by an integrated pyrometer with feedback - the pyrometer can directly adjust the power of the laser source.
Conclusion
The desired quench temperature at the desired speed can be achieved with sufficient power reserve of the laser source and optical configuration. However, when increasing the laser power, it is necessary to determine the emission factor of the material to avoid overheating.
Laboratory Note: Due to the working point size of 0.3 mm, it is necessary to ensure accurate laser point guidance on the hardened cutting edge during operation. Any deviation directly affects the hardening result.