The use of CO2 lasers for high-speed stripping of busbar contacts in the production of electric vehicles. Fast and efficient removal of insulation from electrical busbars using CO2 lasers. Can be easily and quickly integrated into existing automotive production line environments.
As automakers prepare to produce electric vehicles (EVs) in greater numbers, every aspect of their production is being improved. The goal, of course, is to reduce production costs while improving vehicle reliability and performance.
One important part of EVs is the electrically conductive cables that distribute power throughout the vehicle. These are called busbars. Because of the amount of electrical current they must carry, busbars are not just wires. They are thick, ribbon-shaped wires (typical dimensions are in the range of 12 mm wide x 3 mm thick) with insulation around them. The metal itself is most often copper or sometimes aluminium. The insulation is a plastic material (usually polyamide PA12).
Insulated busbar material is often supplied in long lengths on a spool, just like traditional conductors. The automotive manufacturer cuts the coil to the required length and bends it to the required shape. These shapes can be quite complex, as they have to run around various other parts and structures in the car to get the electricity to where it is needed. At some point in production, some of the insulation must be removed (stripped) from both ends of the busbar. This is necessary for the electrical connection to other components. Automobile manufacturers have several specific requirements for this process:
- First, the removal of insulation must be fast to be cost-effective and not limit production. This means removing approximately 25 mm (1 inch) of insulation in a matter of seconds.
- Second, the insulation must be removed completely. This is because residual insulation in the stripped area can interfere with electrical connections, wasting energy (reducing vehicle efficiency). In addition, busbar ends are often welded to other wires or batteries. Any plastic that remains on the surface of the conductor contaminates the weld, impairing its electrical and mechanical properties.
- Finally, the conductor itself must not be damaged by stripping. This could reduce its mechanical strength or increase its electrical resistance, creating a potential failure point.
All these reasons essentially rule out the removal of the insulation by any mechanical method, such as a knife or scraper. It is also difficult to remove insulation from a curved or oddly shaped surface using a knife.
Removing busbar insulation by laser
Given these requirements, lasers are a great tool for removing busbar insulation. This is because the laser process is completely non-contact and can be easily configured to work with curved parts. This makes laser processing fast and flexible. CO2 lasers in particular are ideal for this task. This is because the CO2 laser produces a wavelength beam with specific characteristics. This beam is very strongly absorbed by most plastics used for insulation and is also highly reflected by copper. This means that the laser beam quickly vaporizes the insulation, but once it hits the underlying conductor, it bounces harmlessly back off it (because the copper merely reflects the CO2 laser beam instead of absorbing it). It is therefore easy to remove the insulation while leaving the copper completely intact.
The principle of busbar stripping in manufacturing
For the actual stripping, the laser beam is concentrated to a small point on the busbar where its energy is concentrated. This focused beam is moved back and forth by a high-speed scanner to cover the entire area to be stripped. As a result of the process, the energy of the laser beam vaporizes the insulation in a predefined area.
Introducing laser busbar stripping into production
When introducing laser stripping in a production environment, there are several important practical aspects to consider. For example, it is possible to use two lasers to achieve the required process performance. Each laser removes the insulation from one side of the busbar (so in the picture, the second laser would be coming from below). This also removes the complication of handling the part so that the other side is available for stripping. It is also preferable if the laser beam hits the busbar at an angle. This accomplishes two things. First, it avoids the possibility of the laser beam bouncing back and damaging the laser optics. Second, it allows the laser to remove the insulation from the top and the edge of the busbar at the same time (because the laser beam at an angle "sees" the side of the busbar).
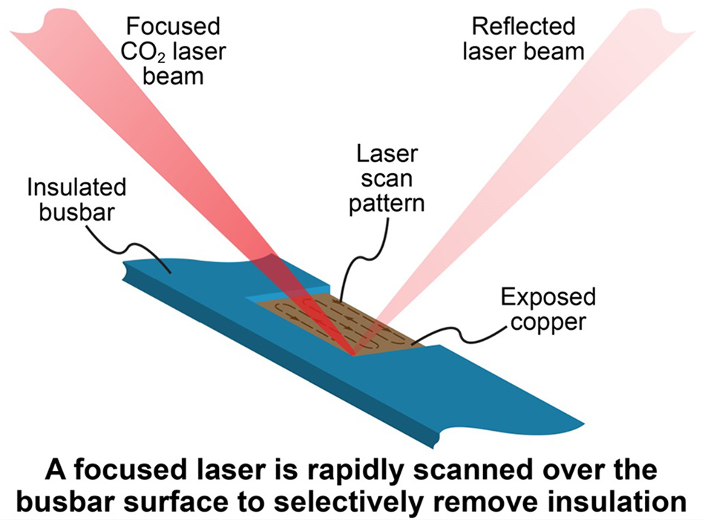
Solving the model case of stripped busbars
Our laser system for busbar stripping is a complete solution. The system includes two PowerLine C subsystems and all associated scanning and beam transmission optics, along with all necessary control electronics and software. The PowerLine C system can remove the polyamide busbar insulation in a 30 mm long, 0.5 mm thick section from both sides of a 6 mm wide busbar in approximately 6 seconds. Removal of the insulation is completed without any damage to the conductor, ensuring a high yield process.
Two different busbar stripping systems are available - an inline version and a stand-alone version.
- The inline system is integrated with a coil feeding mechanism that delivers a continuous strip of busbars. The laser strips it before cutting and final bending. The PowerLine C system also supports "on-the-fly" stripping, where stripping is performed without slowing or stopping busbar movement.
- In a separate version, a robotic arm selects and inserts pre-cut and bent busbars into the system, which are then laser stripped.
See high-speed and efficient busbar stripping in action:
Source: www.coherent.com