The increasing use of polymer parts, especially for high-precision products, is leading manufacturers to seek joining technologies that offer better welds, higher production performance and lower costs. Laser welding of plastics promises to be a boon in all of these areas. However, implementing a laser process to consistently deliver optimal results and minimize costs requires an understanding of the technology. And to achieve this, it's often helpful to work with a supplier who is an expert in it from the product design stage.
Laser polymer welding has several advantages over other joining methods, but its proper implementation requires knowledge of the technology and often benefits from consulting with an experienced equipment supplier early in the product development cycle.
POLYMERS - BOTH PROMISE AND CHALLENGES
Polymers have several unique properties and advantages over other materials. These include high strength-to-weight ratios, mechanical flexibility, corrosion resistance, biocompatibility, electrical and thermal insulation and in some cases even optical transparency. In terms of manufacturing, polymer parts can often be produced by various moulding techniques. These methods offer high production capacity and low unit costs.
All of this has led to increased use of polymers in areas as diverse as packaging, automotive manufacturing, microelectronics and medical devices. A common requirement in many of these applications is the joining of two or more polymer parts in the assembly of a product. For applications involving sophisticated products such as medical implants and electronic sensors, this joining must be performed with high mechanical precision, minimal particle debris formation and excellent bond strength.
In high-volume production, some form of welding is usually used rather than simple bonding. This is because welding can usually be done much faster and more accurately than bonding and produces stronger and more reliable joints.
In practice, many different methods of welding polymers are used. These usually involve selectively fusing the material by heat, friction or vibration, or even by using chemical solvents. Each of these techniques has its own advantages and applications. Laser welding of polymers is becoming increasingly popular for the most demanding applications as it brings a unique combination of benefits. These include:
Precision
- The highly localized application of laser energy causes little or no part deformation, provides small dimensional tolerances, and can be used on complex shaped parts.
Repeatability
- The laser process is inherently highly consistent and can be precisely controlled by process monitoring equipment.
Weld quality
- Weld seams are close and cosmetically excellent (no burrs or drips). Post-processing is rarely necessary.
Weld strength
- Laser welding provides a strong weld that is free of gaps and can provide a hermetic seal.
No contamination
- No additional materials are used in laser welding and virtually no contaminants are generated.
Speed
- The entire welding process is fast and well suited to automation
THE BASICS OF LASER WELDING OF POLYMERS
Laser welding of polymers uses a laser as a heat source to melt the material. There are many different ways this can be done depending on the materials being joined, the specific requirements of the application and various manufacturing aspects. One of the most useful and commonly used techniques is called "transmission laser welding" (TTLW). This method consists of joining one part made of transparent plastic to another that is opaque. In this case, the terms 'transparent' and 'opaque' refer specifically to whether the parts absorb or transmit the wavelength of the laser used, not whether they are visually transparent or opaque.
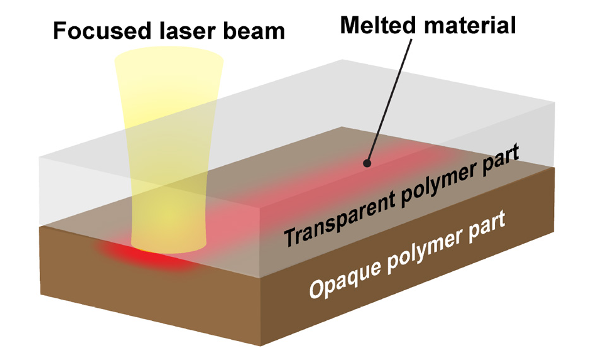
Figure 1: In TTLW, the laser beam passes through the transparent plastic part and is absorbed by the opaque part below. This heats and melts the bottom part, thus welding the parts together.
TTLW can be performed in several different ways depending on the size and shape of the part, the desired pass rate, the desired quality and properties of the weld, and other factors. One of the most useful and versatile methods is called quasi-simultaneous welding.
In quasi-simultaneous welding, two parts are either clamped together or in direct contact, with the free part on top. The laser is directed inwards through the transparent part and downwards towards the opaque part. The opaque polymer absorbs the laser light, heats up and melts. The heat from it also melts part of the clear part.
The laser beam is quickly scanned to draw the pattern of the desired weld. It is usually scanned over the pattern many times and this results in the entire path of the weld being melted simultaneously (hence the name). Once the entire weld path has been melted, the laser is switched off, the molten material solidifies and forms the weld joint. Quasi-simultaneous TTLW is a fast, versatile method that provides excellent joints and high production capacity. It is most useful for welds that are completely flush (flat) or have little elevation change.
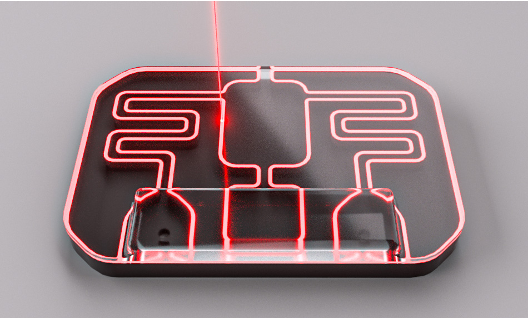
Figure 2: In quasi-simultaneous welding, the laser beam is rapidly scanned along the entire weld path to melt it all at once.
THE RIB COLLAPSE METHOD
One particular part configuration that is often used for quasi-simultaneous TTLW is called the "rib collapse" method. In this case, the lower part has a thin protruding rib that fits into a corresponding groove in the upper part. However, the groove is slightly wider than the rib.
The lower rib is partially melted by the laser during welding, while the clamps actively press the two parts together. Part of the lower rib is melted and this material flows to fill part of the gap between the upper and lower parts. This then solidifies again to form a welded joint.

Figure 3: Schematic of the main steps of the quasi-simultaneous TTLW method with "rib collapse".
This particular version of TTLW is particularly useful because it provides a good weld joint even when the parts are not perfectly straight or strictly fused. In addition, the "collapse height", i.e. the amount by which the top part moves down during welding, can be monitored and used to control the closed loop process. This allows very consistent results to be achieved in batch production, even when parts vary in dimensions or in the absorption of laser energy by the material. Closed-loop process control can even compensate for changes in laser output power or laser focus point characteristics.
STEPS TO SUCCESS
Of course, there are many nuances and considerations when introducing TTLW polymer welding into production. So what is the best way to introduce this technology? In fact, there are three key things to consider before production even begins, and perhaps even right away in the product design cycle.
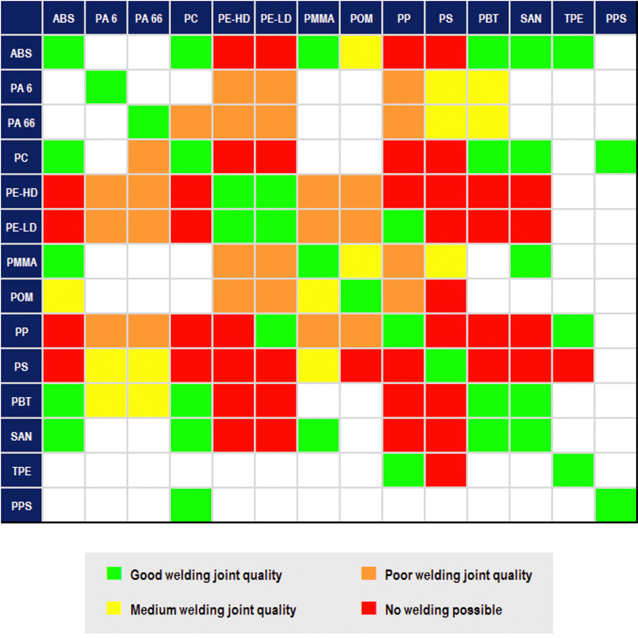
Figure 4: Materials suitable for TTLW welding.
MATERIAL SELECTION
For the method to work, it is essential that there is a certain temperature range in which both polymers (clear and opaque) remain molten but have not yet thermally degraded. The larger this overlap, the wider the process window. And a wider process window makes production easier and more robust. The table summarizes which common polymer combinations are compatible with laser welding.
PRODUCT DESIGN
Another aspect is the issue of "design for manufacturing". For example, the implementation of the collapsed rib method requires that the part design has sufficient space in a suitable location for clamp engagement during welding, while allowing free access of the laser beam to the entire weld path. The dimensions and shape of the rib and groove must also be chosen to provide sufficient material for the welding process and to accommodate the resulting melt. In addition, the parts must be designed to allow sufficient collapse height. For high precision applications, alignment features such as positioning pins may need to be incorporated into the part design. The goal is to achieve a strong weld and good weld cosmetics while eliminating the need for subsequent trimming of eaves or deburring.
CHOOSING THE RIGHT LASER SOURCE AND PARAMETERS
Last but not least, there are all the issues related to process development. This means selecting the right laser source for the polymer materials, determining the optimal laser operating parameters, and determining what process variables need to be monitored or controlled to achieve the desired results. There may also be various practical issues regarding parts handling, mechanical and software interfacing of the polymer welding system with other production equipment, and, of course, acquisition and operating costs.
The easiest way to address all of these factors is to partner with a supplier who can provide application development assistance. Specifically, this means finding a supplier that can perform tests to determine what system configuration will yield the best results and help determine the optimal laser parameters for the manufacturing process. Coherent Labs provides just these services and is also a manufacturer of laser systems for polymer welding that can be easily integrated into a manufacturing environment.
CONCLUSION
In conclusion, laser welding enables precision joining of polymer parts and is a cost-effective method in a wide range of production volumes. It can help deliver on the promise that polymers will reduce costs, save weight and provide advanced functionality across a wide range of products. If an organization does not already have expertise in polymer welding, working with a knowledgeable equipment supplier from the outset will contribute to effective implementation.
Source: coherent.com