Call
Marking the dosage scale on the insulin pen dose dial presents several challenges. First, the accuracy of the marking must be high to ensure that users always receive the correct dose. And second, the mark itself must be sufficiently legible so that the consumer has no difficulty reading it even in poor lighting conditions or with some degree of visual impairment. However, the economics of insulin pen production require the labelling system to be extremely cost-effective and the cost per part extremely low. This translates into the ability to mark with high throughput and operate with minimal operating costs - for any consumable.
"Coherent created a laser marking machine that provided the required performance and reliability, met cost targets and was integrated with the rest of the marking system."
- Teddy Schultz, Sales Director, Masentia A/S
Solution
Laser marking is the only viable option that meets all quality, throughput and cost objectives for this application. Ink marking becomes prohibitively expensive at very high production volumes due to the cost of consumables (ink). In addition, the contact nature of inkjet printing causes uptime and reliability issues. In this particular case, it was also not possible to print the scales directly onto the parts, as the manufacturer produces a number of variations for its own customers, each of which would then require a separate expensive mould. However, despite the inherent advantages of laser technology for this application, the actual implementation of a solution that would meet all the end user's requirements required close collaboration between the supplier of the Coherent laser system, the supplier of the production equipment Masentia A/S (Odense, Denmark) and the machine manufacturer SVM Automatik A/S (Silkeborg, Denmark).
Result
For this application, the requirement for process speed was solved by integrating multiple (four or six) Coherent Powerline E40 laser markers into a single system. The Powerline E40 system includes a 40W diode-pumped solid-state laser (at a wavelength of 1064 nm), a dual-axis galvanometer scanner, scanning optics, control electronics/interface and Visual Laser Marker (VLM) control software. Each machine is controlled independently, allowing simultaneous marking around the perimeter of the part in a single operation, without any rotation or movement of the part. Coherent supplied the laser markers and Masentia provided the design and configuration of the laser module within the overall system. SVM Automatik incorporated the design into the entire machine, designed the machine and manufactured the robotics, including the specific hardware and software required to integrate the machine with the customer's other production equipment. This close collaboration was key to delivering a marking system that met the end user's performance, reliability and cost objectives and could operate in their existing production environment.
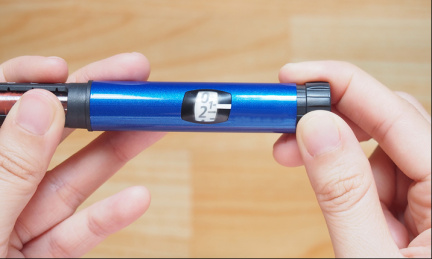
To learn more about SVM Automatik's insulin pen labeling with the Coherent Powerline E40 system, read the full success story.
Source: coherent.com