Different lasers are used for different cutting tasks. Read on to find out how each one excels and what you should look for when choosing the right laser.
Learn how to ask the right questions when choosing a cutting laser to get the capabilities, performance, reliability, price and support that will ensure success in your application.
Table of Contents
- Why use lasers for cutting?
- How to use this laser buying guide
- An overview of precision laser cutting
- Laser cutting mechanisms
- Fusion Cutting
- Ablative cutting
- Remote Cutting
- Checklist for selecting a cutting laser
- Process factors
- Laser factors
- Implementation factors
- Selection guide by material
- Selecting a laser supplier
- Summary
Why use lasers for cutting?
Laser cutting has a number of advantages over other high-precision cutting methods. These include:
- Non-contact processing, which prevents damage to small or delicate parts.
- Zero tool wear, which reduces downtime and tool change costs.
- Highly consistent results.
- Unmatched mechanical precision and the ability to produce fine detail.
- Better edge quality and less debris than other methods, minimizing post-processing.
- Faster than other methods.
- Smaller kerf width.
- High versatility, allowing easy reconfiguration to meet changing production requirements.
For all these reasons, lasers are used in an incredibly diverse range of precision cutting applications. They are used to cut thin glass and sapphire plates for smartphones and tablets, composites, semiconductors, ceramics, nitinol, titanium and steel in the manufacture of medical products, and much more. There are many types of lasers that service this wide range of cutting applications. And sometimes laser manufacturers even create specific models that are optimized for a particular process. Choosing the right laser for your application from this vast array of commercially available products can seem like an overwhelming task. Are you overwhelmed? Don't worry. That's why we've created this buying guide.
How to use this laser buying guide
The purpose of this cutting laser buyer's guide is to help you choose a cutting laser. We won't tell you which laser to buy or which company to buy it from. However, we will provide you with a lot of context so that you will feel confident when you are ready to make a buying decision. More than anything, our goal is to educate you on what questions to ask when you are researching the purchase of a cutting laser.
TIP: The table of contents below lists the main types of precision cutting lasers currently available and is a great place to start your journey. The links embedded in the Overview Table will take you to additional information about the lasers themselves, or directly to sections of this document that offer guidance on which of these technologies is typically best suited for your application. Obtaining this information for specific applications is not always easy, as many suppliers only offer a limited range of laser technologies. As a result, they promote what they have as optimal for each application, whether or not this is the case. Coherent is one of the world's largest laser companies and a global leader in materials and networking as well. We provide services in many cutting applications for the medical device, communications, microelectronics, device markets and more. Most importantly, Coherent manufactures a comprehensive line of cutting lasers. This allows us to provide objective recommendations based solely on your unique needs and project requirements.
But what are your project needs and requirements? The first critical step in the purchasing decision is to correctly identify the aspects that are most important in your own application. The most common of these include:
- Technical factors such as material compatibility, pass rate and cut quality.
- Cost factors such as purchase price, maintenance costs, consumables and operating costs.
- Integration options such as supported interfaces and communication protocols and product size and weight.
- Service, such as geographical availability of spare parts and maintenance and speed of service response.
- Application support, such as vendor willingness to process samples and assistance with process development
For a more detailed discussion of typical considerations when selecting a cutting laser, see the Cutting Laser Selection Checklist.
Overview of precision laser cutting
This table lists the most commonly used cutting lasers for precision applications and summarizes their key features and applications. Its purpose is to allow you to quickly identify the type(s) of laser most likely to be useful for a particular application and narrow your search.
Note: The primary cutting mechanism is listed for each laser type. Technical information on these processes is provided in the Laser Cutting Mechanisms section.
Nanosecond solid-state lasers | Ultra-short pulse lasers (picosecond/femtosecond) | Ultrashort pulse lasers (picosecond/femtosecond) | ||
---|---|---|---|---|
Primary cutting mechanisms | Fusion cutting, Remote cutting |
Ablation, Remote cutting |
||
Output characteristics | Average power range | W - kW | W - 100W | |
Wavelengths | Infrared green | |||
UV | ||||
Energy in pulse | Higher, allowing deeper cuts per pulse, suitable for thick materials | Lower, minimizes thermal damage, better for thin or heat-sensitive materials | Typically lower pulse energies - but extremely high peak powers - allow cold ablation with minimal thermal damage. | |
Pulse length | Greater pulse width means greater heat dissipation into the material | Shorter pulse width means less heat spread into the material | Extremely short pulse duration virtually eliminates heat spread, resulting in the removal of "cold" material. | |
Top performance | Lower peak power, more material melting than evaporation | Higher peak power, better for ablation and accuracy | Extremely high peak power (gigawatts) that allows rapid evaporation without significant melting, ideal for very precise ablation. | |
Pulse repetition rate | Higher, resulting in faster material removal but potential heat build-up. | Lower, reduces cumulative thermal effects, better for delicate materials | medium to high repetition rate depending on the system, allowing fast and accurate processing without significant heating. | |
Beam quality | High beam quality with very precise focus, ideal for micro machining and very precise cuts. | |||
Practical considerations | Cutting speed | Faster due to high repetition rate and energy per pulse. | Slower but more controlled, focused on precision | Faster but dependent on material and pulse repetition rate, for very precise jobs, often slower. |
Thermal waste | Greater thermal accumulation, possibility of a larger heat affected zone (HAZ) | Lower thermal impact, smaller HAZ, cleaner cuts | Minimal thermal impact; negligible heat affected zone into the material | |
Maintenance | Requires regular maintenance | Minimal, robust, high uptime | Generally low maintenance, but systems can be complex and costly to maintain. | |
Material compatibility | Metals, Ceramics, Polymers, Composites, Semiconductors |
Metals, Glass, Ceramics, Composites |
Metals, Ceramics, Polymers, Glass and transparent materials, Semiconductors |
|
Key findings | Best for thicker metals, ceramics and harder materials and fast cutting (e.g. orthopedic implants, thicker semiconductors). | Best for thin metals, polymers, semiconductors and heat sensitive materials and for high precision cutting (e.g. stents, wafer slicing). | Best for high precision tasks such as cutting semiconductors, thin films, glass, polymers or advanced medical devices where heat damage must be avoided and post-processing is not required. |
Laser cutting mechanisms
All solids are held together by bonds or attractive forces between the atoms, ions or molecules that make up the material. At the most basic level, cutting any solid requires breaking these bonds. In traditional mechanical cutting, such as with a saw or knife, the cutting tool exerts a force on the material in a region centred around the edge of the tool. This creates shear, which breaks the bonds between the particles on which the force is applied and adjacent particles on which the force is not applied. If the force is large enough, the bonds are broken. This is a fundamental physical process that occurs whether it is cutting paper with scissors, cutting wood or carving roast meat.
Lasers are non-contact tools. They do not exert any physical force on the objects they illuminate. Instead, they make the cut by entirely different mechanisms. Yet they must achieve the same end result, namely, breaking atomic or molecular bonds in a contiguous region to create a cut.
Laser cutting can be divided into three main categories:
Reactive or flame laser cutting is generally not used for high precision applications. The other three methods are described in detail here.
Fusion cutting
In fusion cutting, the laser heats the target material to the melting point, creating a molten bath. At the same time, a high-pressure auxiliary gas (usually nitrogen or in some cases argon) is conducted with the laser beam to push the molten material out of the cutting area. The auxiliary gas also helps to cool the cut area, preventing oxidation and ensuring cleaner edges. This method offers remarkable accuracy and is ideal for creating complex, burr-free cuts in metals, ceramics and some polymers.
One of the key advantages of fusion cutting is its ability to maintain fine tolerances and achieve smooth, high-quality edges. This is essential for components such as stents, surgical instruments or microelectronics. These applications require not only dimensional accuracy, but also minimal thermal damage to the surrounding material. Any excessive thermal influence can degrade performance or require costly additional processing.
Fusion cutting is particularly suitable for materials such as stainless steel, titanium and silicon wafers. The use of a non-reactive auxiliary gas such as nitrogen ensures a clean cut without compromising the integrity of the material. With gas pressures ranging from 75 to 250 psi, fusion cutting can handle both thin and thick materials, depending on the specific requirements of the application. The precision, combined with the ability to cut complex geometries, makes fusion cutting an essential technology for industries where accuracy, cleanliness and efficiency are key.
Ablative cutting
Ultra-short pulse lasers (picosecond and femtosecond) provide a unique cutting method due to their extremely short pulse duration and very high peak powers, reaching gigawatt levels. Since the pulse duration is shorter than the "conduction time" of the material, extremely rapid and localized heating occurs, instantly converting solid material to vapor. The steam is then blown out of the cut by a coaxial auxiliary gas, usually argon.
This ablative cutting method ensures the highest possible quality cutting edges with excellent dimensional accuracy and no burrs. The absence of burrs is crucial for applications such as cutting nitinol tubing for medical devices or stainless steel and titanium for luxury watches, as the resulting cuts require minimal post-processing.
Remote cutting
The main difference between remote cutting and other methods is the location of the laser head, which is remote from the work surface. The scanning head moves the beam across the material at very high speeds (>1 m/s). No auxiliary gas is used in this method. Depending on the thickness of the material, the scanning head may follow the same path multiple times to produce a through cut. The cutting mechanism itself works on the principle of melt ejection: the laser melts but also partially vaporises the material, while the vapour expansion pressure pushes the melt out of the cutting area.
The cutting paths in this method are usually simple, such as circles or squares, which allows high cutting speeds to be achieved. Distance cutting is most commonly used for thin materials such as battery foils or thin plastic films less than 0.01" (0.25 mm) thick. The laser sources must have sufficient power to melt and vaporize the material.
Checklist for selecting a cutting laser
Cutting Laser Selection ChecklistThese tables are your guide to selecting the right cutting laser. They list some of the key factors that can influence your selection and help you determine what is really important for your particular application. Use them to formulate questions to ask yourself when considering a particular laser type and supplier.
Process factors
Process FactorsLaser selection almost always begins with identifying and defining the process requirements and desired outcome.
Factor | Notes |
---|---|
Material type | Material properties usually play the biggest role in selecting the right laser cutting machine. The most important are generally the linear absorption properties of the material (what wavelengths it absorbs), reflectivity, thermal conductivity and melting point, especially when using nanosecond solid-state and nanosecond fiber lasers. The overview table provides a good starting point for matching the laser to the material. |
Material thickness | The thickness of the material and the required cutting speed usually determine the required laser power. Thicker materials usually require higher power and lower cutting speeds to ensure clean cuts. |
Required speed | There is often a trade-off between speed and cut quality. Higher speeds can reduce accuracy, so you need to balance speed with the desired cut quality. |
Heat-affected zone (HAZ) |
Minimizing the HAZ is a critical parameter for cutting heat-sensitive materials and small parts. USP lasers ensure the minimum achievable HAZ. |
Cut/edge quality | Some laser/material combinations tend to provide smoother cutting edges and fewer micro-cracks. Both can affect the subsequent mechanical strength of the cut part. Smoother edges can also reduce the need for post-processing. Keep in mind that the polarization of the beam relative to the direction of the cut can have a large effect on the quality of the cut. |
Production of dirt | Large amounts of debris can increase cleaning time and require multiple post-processing steps. |
Post-processing | The need (or lack thereof) for post-processing can dramatically affect the overall process cost and throughput. Some types of post-processing can also have a significant environmental impact. |
Laser factors
After defining the process requirements, the next step is usually to select the right laser technology. In many cases, the technical requirements of the process - the material, its thickness, the required throughput and more - will narrow the selection to a single laser type.
Factor in | Notes |
---|---|
Output power |
A certain minimum output is often required to cut a specific material and thickness. Increasing the power above this limit increases throughput, but can also increase cost, as higher laser power tends to be more expensive. In some cases there is an optimum power level, exceeding which can have negative consequences such as a larger heat affected zone (HAZ), reduced cut quality or increased debris production. This is one of the reasons why "multi-pass" cutting, where the laser repeatedly traverses the same area to create a through cut, is often used with both nanosecond solid-state and USP lasers. |
Wavelength |
The wavelength of the laser is a key factor for two reasons. First, matching the laser wavelength to the absorption properties of the material optimizes cutting efficiency, speed and often the quality of the cut. The following table summarizes the compatibility of lasers with common materials. Second, shorter wavelengths typically allow for higher cutting accuracy because they can be focused to a smaller point. Depending on the optics of the beam, shorter wavelengths can also provide greater depth of field, increasing process stability. |
Beam quality (M² or BPP) |
Beam quality determines how well the laser can be focused. This has two important implications. First, a smaller focus point (lower M² or BPP) allows for a narrower cutting gap and the production of finer, more detailed features. Second, for a given laser power, a higher power density at the focus point can be achieved if the beam quality is improved. Higher power density means that more energy is delivered to a specific area, increasing the ability to efficiently melt or vaporize the material. Better beam quality usually increases the overall power availability of the laser. |
Output mode (pulsed or CW) |
The choice between pulsed or continuous wave (CW) laser depends on the material and the desired results. In addition, some laser types operate in only one of these modes. Overall, CW lasers are usually preferred for applications requiring high speed and throughput when cutting thick or dense materials, such as in the automotive and energy industries. Pulsed lasers excel at precision cutting with minimal thermal impact and processing specialized materials. They are often used for cutting fine or temperature-sensitive polymers, ceramics and thin metals in the e-mobility, semiconductor and medical device industries. |
Beam distribution |
Beam distribution options such as fibre or free-spread optics have a significant impact on the configuration of the laser cutting system and the associated costs. Fiber optic distribution provides tremendous flexibility and makes it easy to integrate the cutting laser into space-constrained production environments along with other equipment. It also simplifies maintenance through improved laser availability. CO₂ lasers cannot use optical fibre for beam distribution, leading to more complex systems that can be subject to optical path "detuning" over time. |
Operational consistency |
Inconsistencies in laser output power can lead to inconsistent cuts, negatively affecting product quality and increasing waste rates or the need for rework. Lasers with consistent output characteristics minimize maintenance downtime and ensure continuous operation and productivity. As production volumes increase, it is critical to know how the laser manufacturer ensures and guarantees operational stability. |
Cooling requirements |
Lasers often require cooling systems using air or water. Water cooling may require specific infrastructure within your operation, which carries additional costs. |
Operating costs |
Many cutting lasers use consumables such as gases (especially assist gases), optical components, and protective windows. Different types of lasers also have specific maintenance requirements and varying levels of reliability. High production volumes can cause the cost of downtime - whether planned or unplanned - to exceed the purchase price of the laser itself. Therefore, it is important to have realistic expectations of laser uptime and reliability and to have a good understanding of the manufacturer's warranties and lifetime specifications. |
Implementation factors
Many laser manufacturers offer similar products - or at least products that appear to be similar. Practical considerations related to cost, integration factors, application development, and follow-up support must be taken into account for final selection. These factors often determine the choice of a particular vendor
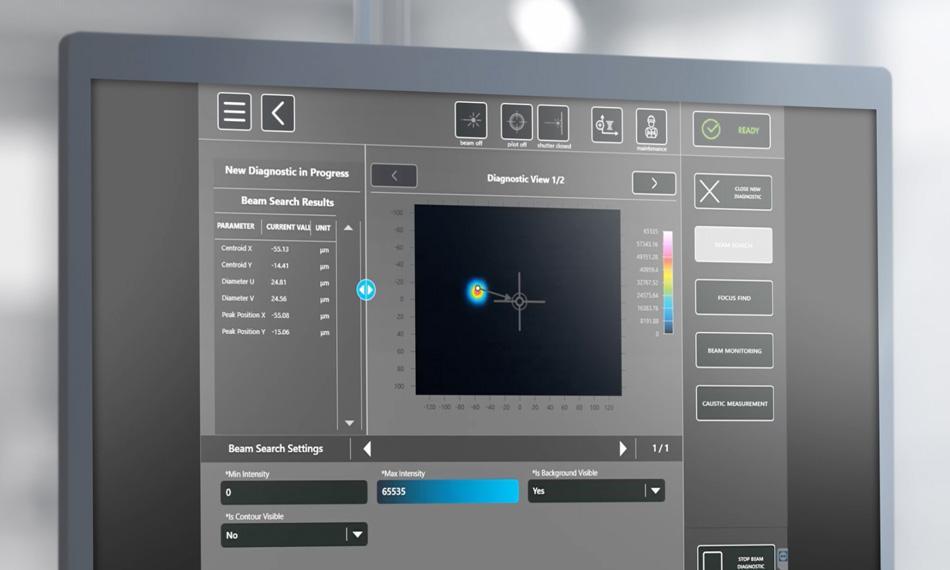
The actual productivity of a laser cutting system in real operation is often determined by the human-machine interface (HMI).
Factor | Notes |
---|---|
Application development | Supplier support in developing and optimizing your cutting process can be invaluable. Look for laser suppliers that offer sample processing and assistance with process development. |
Acquisition costs | Consider the capital cost of the laser, including installation and commissioning costs. Staff training costs can also be a significant factor. |
Operating costs | Evaluate ongoing costs such as maintenance, consumables and energy consumption. Some lasers have lower running costs, which can save money in the long run. Downtime should be considered, which can be a greater risk and cost than the purchase price of the laser. |
Service and support | Evaluate the geographic availability and usual response time for service and support from potential suppliers. Also consider the availability of spare parts to minimize downtime for repairs or maintenance. |
Software | User-friendly and versatile control software can greatly increase productivity and ease of use. Make sure the software is compatible with your existing systems. |
Integration | Easy integration of the laser into your existing production line or machinery is essential. Look for lasers with flexible interface options and comprehensive integration support, and make sure your communication and integration protocols are supported. |
Ease of use | A user-friendly human-machine interface (HMI) reduces training time and operational errors. Prioritize systems with intuitive controls and clear operating instructions. Find out if the laser supplier offers training. |
Selection guide by material
The choice of a particular laser cutting technology is almost always determined by the material - its absorption properties and thickness, along with factors related to cutting speed and the quality of the cutting joint. This table lists some common materials and the types of lasers typically used to cut them.
Class of materials | Class of lasers | Main characteristics | Comment |
---|---|---|---|
Metals | Nanosecond fibre lasers | High power density enables fast cutting and processing of thicker materials. | Particularly suitable for thin to medium thickness metals, providing a good balance between speed and accuracy. In addition, the output in the green and UV region improves the processing of reflective metals such as copper and aluminium, minimising the heat affected zone (HAZ) and ensuring clean cuts. |
Nanosecond solid-state lasers | Provide precision for complex cuts on thin substrates. | Ideal for precision cutting of thin metal substrates with high accuracy requirements. With green (532 nm) and UV (355 nm) wavelengths, they improve absorption in reflective metals, reducing thermal deformation and improving edge quality. For thicker metals, however, they are less effective than fiber lasers. | |
Ultrashort pulsed lasers | Highest possible precision, suitable for very delicate parts. | Lower speed limits these lasers to the most demanding, precise and heat sensitive applications. | |
Polymers | Nanosecond fiber lasers | Effective for cutting polymers with high absorption at the fiber laser wavelength (typically 1064 nm), but thermal effects such as melting and discoloration are more pronounced compared to ultrashort pulse lasers. Fiber lasers are best used for thicker or less heat-sensitive polymers. | Potential for melting and burning - varies by material. |
Nanosecond solid-state lasers | Precise, clean cuts with minimal thermal distortion and HAZ | The combination of edge quality and minimal HAZ is particularly useful in microelectronics and medical device manufacturing. | |
Glass | Nanosecond fibre lasers | Efficient cutting with a moderate heat affected zone, but require careful handling to avoid chipping. | Often used in industrial applications where speed and precision cutting of thin glass is important. |
Nanosecond solid-state lasers | Produce fragments in the sub-micrometer range and allow cutting of arbitrary shapes. | Cutting is typically performed in the green (532 nm) or UV (355 nm) region using a bottom-up technique, where the laser enters through the top surface and focuses on the bottom surface of the material. | |
Ultrashort pulsed lasers | Provide extremely high precision and allow cutting of any shape including cut-outs. Shards can reach sizes of hundreds of nanometers, often eliminating the need for post-processing. | They typically use infrared wavelengths (1064 nm) and "filamentation" techniques such as Coherent SmartCleave. | |
Ceramics | Nanosecond fibre lasers | Can be used to cut ceramic materials with good speed and accuracy, although thermal effects can be more pronounced than with ultrashort pulsed lasers. | They are used where speed and accuracy need to be balanced, for example when cutting tiles or advanced ceramic materials. |
Nanosecond solid-state lasers | These use infrared, green or UV lasers depending on the material, required accuracy and heat affected zone (HAZ). | They provide a good compromise between cutting speed and accuracy. | |
Ultrashort pulsed lasers | Highest precision and smallest heat affected zone (HAZ) but with the slowest cutting speed. Can use infrared, green or UV lasers. | Suitable where minimizing thermal impact is key, such as medical device manufacturing, microelectronics and advanced manufacturing processes. | |
Semiconductors | Nanosecond fibre lasers | Used for medium precision tasks where speed is a priority and material thickness allows for some thermal effects. | Suitable for cutting thicker semiconductor wafers where speed is more important than minimizing thermal effects. |
Nanosecond solid-state lasers | Use infrared, green or UV lasers depending on the material, required precision and heat affected zone (HAZ). | They provide a good compromise between cutting speed and accuracy. | |
Ultrashort pulsed lasers | Offer the highest precision and the smallest heat affected zone (HAZ) but the slowest cutting speed. They can use infrared, green or UV lasers. | Ideal for cutting thin substrates or creating complex patterns without causing thermal damage. | |
Composites | Nanosecond solid-state lasers | Use infrared, green or UV lasers depending on the material, required precision and heat affected zone (HAZ). | Effective for detailed and complex cutting of composite materials used in the automotive, aerospace and industrial sectors. |
Ultrashort pulsed lasers | Provide the highest accuracy and smallest heat affected zone (HAZ), but with the slowest cutting speed. They can use infrared, green or UV lasers. | Suitable for high precision cutting of composites where minimising thermal impact is essential, for example in aerospace and medical applications. |
Choosing a laser supplier
The success and efficiency of a laser cutting system in a real production environment depends on several factors that go beyond the interaction of the laser with the material itself. These factors include integration capabilities, service and support, assistance with application development, and the overall reputation of the supplier. These aspects can affect capital costs, operating expenses, downtime, and the need for operator training and maintenance.
Key factors in selecting a laser supplier
Integration options
- Supported interfaces and communication protocols
- Importance: Seamless integration of the laser system with your production line and existing equipment is essential. Compatibility with control systems and communication protocols can significantly impact operational efficiency.
- Consider: Verify that the supplier supports common industry protocols such as Ethernet, Modbus, PROFINET, etc.
- Equipment size and weight
- Importance: The physical parameters of a laser system can affect its placement and integration into tools such as robotic arms.
- Consider: Consider the size of the system, its footprint and weight with respect to your space. Compact and lightweight systems are ideal for confined spaces.
- Ease of use
- Important: User-friendly HMI and intuitive controls reduce operator training time and the likelihood of errors.
- Consider: Evaluate the interface for ease of navigation and clarity. Training and vendor support can further facilitate system use.
Service and support
- Availability of spare parts and maintenance
- Importance: Quick availability of parts minimizes downtime and supports continuous operation.
- Consider: Make sure the supplier has an accessible service center and spare parts warehouse in your region.
- Speed of service response
- Importance: Rapid response to problems is key to maintaining high productivity and reducing losses.
- Consider: Verify average response time and ability to provide on-site support.
- Reliability and warranty
- Importance: Warranty and system reliability affect long-term operating costs and operational confidence.
- Consider: Check the warranty terms and historical reliability ratings of the vendor's systems.
Application support
- Sample processing
- Importance: Testing material samples will allow you to assess the performance of the laser and its suitability for your application.
- Consider: Prefer suppliers who offer sample processing as part of their pre-sales support.
- Process development support
- Importance: Optimizing cutting parameters increases production efficiency and quality.
- Consider: Select a supplier that offers process development and integration support.
- Training and documentation
- Important: Quality training and clear documentation ensure smooth operations and minimize downtime.
- Consider: Make sure the supplier provides training, user manuals and maintenance guides.
Supplier's overall reputation
- Experience and expertise
- Importance: The expertise of the supplier ensures its ability to meet the demanding requirements of the application.
- Consider: Research the company's history, references, and the variety of applications supported.
- Customer reviews and references
- Importance: The experience of other customers provides important information about the reliability and support of the supplier.
- Consider: Look for reviews and case studies relevant to your industry.
Summary
Choosing the right laser supplier requires careful consideration of more factors than just technical specifications. Integration capabilities, service support, process development assistance and overall supplier reputation are key.
Laser technology offers unparalleled precision and flexibility, which is essential for trends such as miniaturization, increased functionality and lower costs. This guide helps you understand laser selection and supplier selection to optimize your manufacturing processes.
For a successful and efficient implementation, it is essential to work with a supplier that offers not only technology but also comprehensive support. With expert application development and fast service response, you will achieve the best results and ensure long-term success.