The combination of sealed CO₂ and UV solid-state lasers enables cost-effective stripping and cleaning of hairpins with the high quality required for mass production of electric motors.
EV manufacturers are under increasing pressure to optimize operations and reduce costs while improving quality. These efforts are key to the necessary expansion of EV market share, especially in high-volume markets where total cost of ownership (TCO) is highly sensitive and where ICE vehicles still predominate.
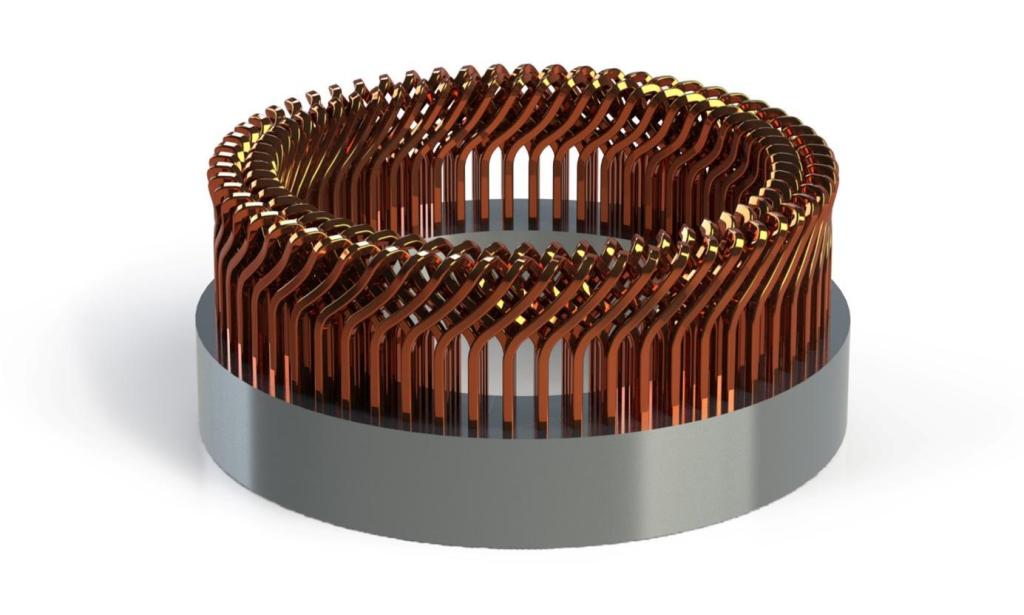
Example of welded hairpins
One opportunity for EV engine manufacturing is to optimise the welding of hairpins - a process that is critical to engine reliability and performance. This approach is proving to offer EV manufacturers a cost-effective way to achieve superior weld quality. Traditional mechanical stripping methods are often insufficient, leading to process inefficiencies such as surface damage, tool wear and production delays that increase costs and impact process reliability.
Understanding the details of the two-phase laser process, which combinesCO2 and UV lasers, is key to achieving optimal results for stripping and cleaning hairpins in electric motor manufacturing. This innovative approach, developed by Coherent, offers significant advantages in accuracy and efficiency. For detailed information on this technology and its practical applications, we invite you to read our more extensive article in the Educational Articles section. Here you will learn more about the principles, benefits and implementation of this approach in electric vehicle manufacturing.
Read more in the article Innovative Coherent laser technology for efficient EV engine welding.