In the rapidly expanding EV industry, EV manufacturers are facing increasing pressure to optimise production processes and reduce costs without compromising on quality. One key aspect is the efficient stripping and cleaning of hairpins - the delicate conductors in electric motors where traditional mechanical methods often run up against their limits. Coherent brings an innovative two-phase laser process that combines CO₂ and UV lasers to offer a high quality and cost-effective solution for the mass production of electric motors.
The hairpin barrier
The windings of electric motors are usually made up of individual copper wires. These are bent into a "U" shape (hence the name "hairpin") and then placed in an assembly. The ends of each adjacent hairpin are then welded together to electrically connect them to form a single continuous winding. In addition, some alternative designs use a continuous flat wire formed into a wave pattern (called a wave winding or S-winding) that is inserted into the stator grooves before welding.
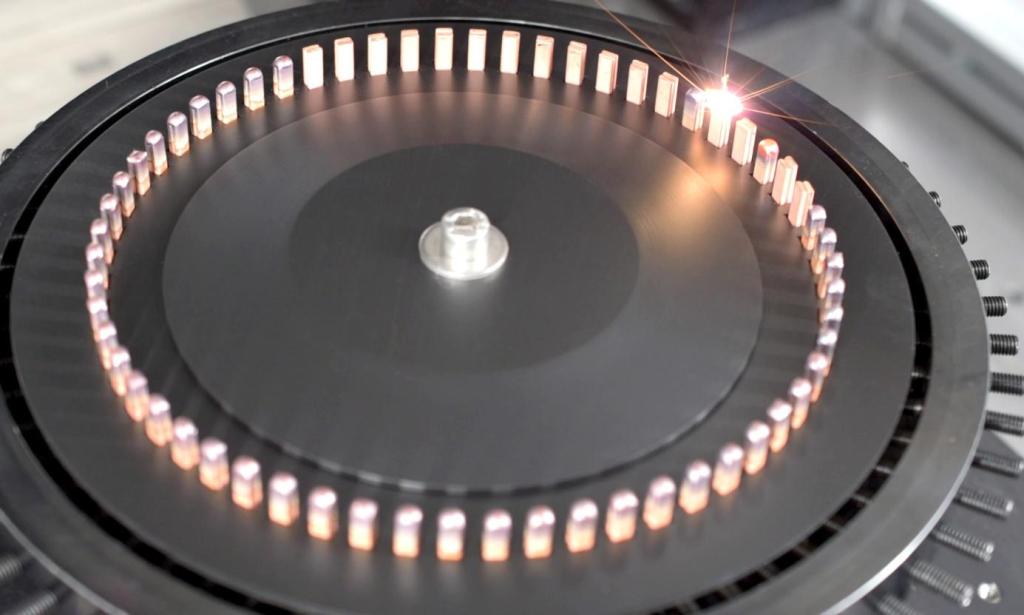
Example of laser welding of pairs of hairpins using Coherent's ARM HIGHmotion 2D fiber laser scanner.
The windings are insulated on all electric motors. For fiber motors, the insulation must be thicker and more robust to accommodate their compact design and the high-voltage requirements typical of electric motors.
A small amount of this insulation must be removed from both ends of each hairpin before welding. This is critical to ensure quality electrical and mechanical connections.
Traditionally, this task has been carried out primarily by mechanical methods, but a single-stage laser process with infrared (1um) pulsed lasers is also used. Mechanical stripping involves the use of a cutting tool in direct contact with the conductor surface to scrape off the insulation. Although these approaches have been standard for years, they present significant challenges in the fast-paced world of electric vehicle (EV) manufacturing.
For example, the physical contact required for mechanical stripping removes a layer of copper from the pin, leaving a textured surface that causes gaps and part-to-pin fit issues, compromising weld integrity and consistency. In addition, wear and tear on the mechanical tools leads to process inconsistency, frequent maintenance, unplanned downtime and potential production interruptions. These problems are compounded by the lower speed of the process, which struggles to keep up with the high-volume demands of electric vehicle production.
Laser stripping in 2 steps is a class above
Lasers are used to strip material in a wide range of applications, including stripping insulation. In this context, the advantages of laser processing include:
- Better weld quality: complete removal of insulation without any damage to the copper wire provides a clean surface for optimum weld quality.
- The absence of tool wear and the elimination of the possibility of machine jams ensures an uninterrupted production flow.
- Increased throughput: Continuous stripping during wire feeding increases production efficiency.
- Increased consistency: without wear or contact, the laser process is stable and reproducible.
It is clear that laser processing can deliver process improvements. However, the real question is which laser is best. In other words, which of the many possible laser sources and implementations that could perform this process provides the best balance of quality, speed and cost for high-volume production of electric motors?
Optimising the laser process
As a leading supplier of nearly all types of industrial lasers, Coherent is uniquely positioned to objectively explore this application without any inherent preference for one technology.
In fact, they haven't found a single best laser for hairline stripping. Instead, our application engineers have developed a dual-laser process to achieve optimal coating removal. Today, this approach delivers the best surface quality before welding at the lowest cost to our customers. The main motivation for investigating the dual-laser process was to overcome the problems of single-stage laser hair removal.
Single stage laser processing is a compromise between coating absorption and underlying copper. A fiber laser wavelength close to 1 µm is not readily absorbed by the coating, resulting in heating at the interface and flaking of the coating onto airborne particles. The particles can interfere with the incoming laser beam and affect pin cleanliness and can become trapped in the system, leading to frequent downtime for equipment cleaning. In addition, the penetrating infrared beam of the fiber laser will not be able to fully remove the polymer residue from the copper surface. It can melt the surface of the copper wire and expose the polymer insulator components such as hydrogen and carbon on the surface. This may contaminate the surface and affect the subsequent quality of the weld.
Coherent's two-step laser hairpin preparation process includes:
- Bulk stripping: most of the insulation is quickly removed using a medium power CO₂ laser. This type of laser is ideal for high-power stripping of non-metallic materials.
- Final Cleaning. This produces a clean surface for welding. The short wavelength UV solid-state laser excels at high-precision material processing and is particularly effective at removing a wide range of materials including polymers, other organic materials and copper.
For the bulk stripping step, the Coherent J-5-10.6 µm laser has proven to be an ideal source. Although a number of different materials are used for fiber stripping (including polyimide, polyetherimide, polyester, polyesterimide, polyamide, polyether ether ketone, epoxy resins, and various fluoropolymers), all strongly absorb the 10.6 µm output wavelength of this laser. For all of these materials, the absorption at 10.6 µm is higher than other available CO₂ laser wavelengths we offer, such as 9.4 µm and 10.2 µm.
Coherent J-5-10.6 µm also has desirable practical properties. It is a fully encapsulated pulsed CO₂ laser that produces an average power of over 400 W, which means it can perform high power stripping. In addition, it is a self-contained and compact package that is ideal for integration into automated equipment.
For the final cleaning step, the Avia LX 355-30-60 HE demonstrates the right combination of output parameters. It is a triple-frequency diode-pumped solid-state laser that delivers an average power output of 30 W at a wavelength of 355 nm. Most importantly, it supports operation at repetition rates up to 300 kHz and pulse energies up to 500 µJ. This enables high-precision ablation at the speeds required for this application.
The Avia LX 355-30-60 HE is also designed for easy integration. The incorporation of the Coherent PureUV™ active laser cleaning motor ensures exceptional durability and maintenance-free operation.
Welding results
The application lab investigated a number of different processes before arriving at the two-phase combination just described. Various lasers, including CO₂, nanosecond pulsed IR fiber lasers, and nanosecond UV lasers, were investigated individually and in combination. The results of processing isolated fibers were analyzed in detail and specific process parameters were optimized after identifying the most promising sources.
As part of the testing, X-ray photoelectron spectroscopy (XPS) was used to analyze the chemical composition of the surface in order to characterize and quantify contaminants. Here we found that a two-step laser removal process (CO₂ combined with UV laser) was the most effective means of removing all residual elements from the copper surface prior to laser welding.
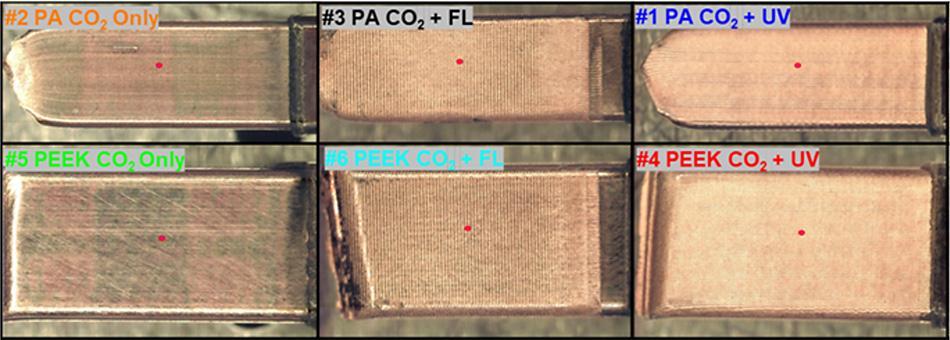
This series of photographs compares different removal techniques using CO₂, ns IR fiber (FL) and ns UV solid-state lasers. In the top row of photos, the insulating material was polyamide (PA) and in the bottom row polyether ether ketone (PEEK). Even a purely visual examination shows that the combination of CO₂ + UV laser appears to be the best in both cases. This was confirmed by actual welding tests.
The most important indicator is of course the quality of the welds obtained after removal of the coating. The next graph shows a series of X-ray images of the welded fibers. It can be seen that the two-step process (CO₂ + UV laser) ultimately produces better quality welds. The two-step CO₂ + UV laser coating removal process minimizes weld porosity by removing polymer residue on the surface prior to welding. Polymer residues are known to contain hydrogen, carbon and other organic elements that can enter the molten metal pool in the liquid state and form pores during weld solidification. The porosity affects the mechanical and electrical properties of the weld.
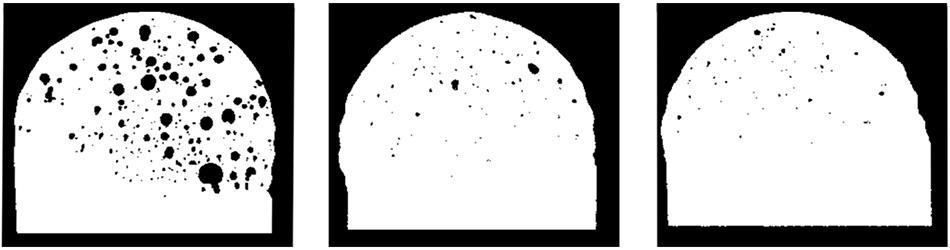
X-ray images of weld beads using three removal strategies. The CO₂ + UV solid-state laser clearly shows the highest weld quality (lowest porosity content).