Coherent Adjustable Ring Mode (ARM) fiber lasers enable welding of high-strength steel and other materials in lightweight automotive seat structures.
When most of us think about car seats, we usually think about comfort and color choices, or options like built-in heating or massage. But for the engineers who design and build car seats, there's much more.
First and foremost, of course, is safety. The driver and passengers are literally strapped into their seats. In a crash, the mechanical strength of the seat structure is the first line of defense to protect the vehicle's occupants and prevent injury.
The other side, however, is weight. In fact, making the structure stronger usually means making it heavier. And car manufacturers are under enormous pressure to reduce vehicle weight. This improves fuel efficiency, reduces emissions from internal combustion engines and increases the range of electric vehicles. Weight is such a big problem in the automotive industry that there is even a discipline of its own - 'vehicle lightweighting' - to address it.
Lightweighting with high strength steel
How do you make car seats that are both strong and light? The key is to use materials that are inherently stronger - such as steel, titanium and magnesium alloys - so that individual components can be made thinner and lighter without sacrificing mechanical strength. And for parts that do not contribute significantly to the strength or stiffness of the seat, use plastics, composites or other truly lightweight materials.
One of the latest developments in car seat construction is the use of high-strength low-alloy steel (HSLA) and advanced high-strength steel (AHSS). These materials have an even higher strength-to-weight ratio than other steels, making them really useful in achieving lightweighting goals. Car manufacturers have been using them for some time in the manufacture of frames and now they are making their way into seats.
Welding high-strength steels is challenging
Modern car seats are made up of a relatively large number of individual parts assembled into complex structures. Metal and other materials are sometimes even combined into multi-layered composites.
Scanning laser welding (where the laser processing head is a considerable distance from the part) has proved to be a very useful tool for their manufacture, for several reasons. Firstly, it can easily process complex three-dimensional shapes of seat components. And in particular, when using a fiber or solid-state laser of several kW, it provides uniform, consistent welds with the penetration depth needed to join multiple layers of thick, layered metal. It is also a fast and flexible method.
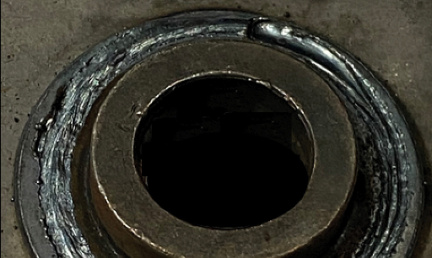
However, there are challenges when welding high-strength steel with traditional fiber lasers. One of them is spatter. Spatter creates a weld with higher porosity and defects, which means low mechanical strength. As welding speed increases, spatter worsens, limiting production performance.
Another problem is inconsistent weld depth. The result is a weld that does not have the same mechanical strength along its entire length.
Material cracking is also a problem with traditional fiber lasers, again reducing mechanical strength. Cracking occurs when the material cools too quickly. It usually occurs at the end of the weld joint where the laser power has been suddenly switched off.
Another problem with rapid cooling of high strength steel is that sometimes a crystalline form called martensite is formed. Martensite, while strong, is the most brittle form of steel. This means that it can crack if too much stress is applied.
ARM fibre lasers do not crack under welding pressure
The key to avoiding all these problems is to spread the laser energy over a larger area and to control the laser energy distribution over that area more precisely. This allows the temperature gradient and the cooling rate of the material to be controlled more carefully. When done correctly, spatter, cracking and martensite formation are eliminated.
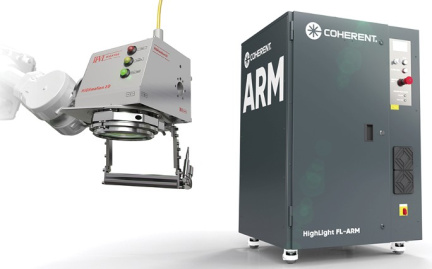
Recently, a major automotive seat manufacturer asked Coherent Labs to perform a series of welding tests on high-strength steel materials. Specifically, this involved welding HSLA sheet metal of various thicknesses using Coherent's HighLight FL8000-ARM fiber laser. A special weld termination mode was used that independently reduced the power in the center and ring beam.
This testing successfully demonstrated spatter- and crack-free welds at process speeds up to 8.8 m/min for the thinnest material combination (2 mm total thickness) and 6.3 m/min for the thickest (5.7 mm total thickness). These speeds are significantly faster than those achievable with traditional fiber lasers. In all cases, weld penetration was very uniform due to the closed-loop power control and the inherent insensitivity of the Coherent FL-ARM laser to back-reflection.
These test results show that the Coherent HighLight FL-ARM laser can provide high quality welds with low incidence of defects in high strength steels. The high throughput achieved and the inherent reliability of this fiber laser technology make it a cost-effective solution for automotive seat manufacturing applications. Want to learn more about this application? Then read the details in our Solution Brief here.
Source .