Although fibre lasers are the dominant laser source for welding, their infrared output is strongly reflected from some metals, particularly copper, which limits their effectiveness on these materials. As a result, high-power solid-state green lasers have emerged as a possible alternative for welding copper, as these wavelengths are more strongly absorbed by the copper metal. However, green lasers have several practical limitations that ultimately lead to higher acquisition costs. This paper reports the results of recent copper welding tests that were successfully conducted with a new type of adjustable ring mode (ARM) fiber laser with a high center beam brightness. The high brightness ARM laser here provided excellent weld quality and better penetration at various welding speeds than commercially available greens. The results suggest that this technology could provide advantages in cost, reliability, and practical applications of fiber lasers for copper welding.
E-mobility manufacturing
The expansion of e-mobility manufacturing is a major factor leading to a significant increase in demand for copper welding solutions. Copper has a number of desirable electrical, thermal, mechanical and cost properties compared to other metals and is therefore used in all e-mobiles - in electric motor stators, in the distribution system (busbars, etc.) and in batteries. The manufacture of many of these components and systems involves welding copper.
However, as well as the high electrical and thermal conductivity that makes copper ideal for these applications, it is challenging to weld with traditional fibre lasers. Specifically, its electronic properties make it highly reflective in the near-infrared wavelength of fiber lasers. And its excellent thermal conductivity requires the delivery of large amounts of laser energy to melt the material and start the welding process.
As a result, when using a traditional fiber laser, very high power is typically required to achieve the power density needed to initially melt the material. However, this "brute force" approach makes the welding process unstable and extremely sensitive to minor variations in the working surface. In particular, the presence of localised surface oxidation or small-scale surface structure inhomogeneities can lead to process instability. The end result can be inconsistent welds with pores and poor surface quality.
Semiconductor green lasers
Copper is almost an order of magnitude more absorbent in the green laser than in the near-infrared region. Therefore, the energy of the green laser can be more effectively coupled to the workpiece, resulting in a more stable and less sensitive welding process than is possible with traditional fiber lasers. As a result, several manufacturers are using high-power solid-state green lasers, and many others are testing and evaluating them.
However, the deployment of high-power green lasers in e-mobility manufacturing faces some significant practical challenges. Some of these stem from the characteristics and design of green lasers themselves.
The laser materials used for solid-state green fiber or disk lasers produce near-infrared light; frequency doubling is used to convert the infrared light to green output. While this process has been used with great success at lower powers, it is starting to run into some difficulties at kW powers. Specifically, the frequency conversion process itself has an efficiency of only about 50%. Thus, to achieve the output power of a 2 kW green laser, a 4 kW single-mode infrared laser is needed. The unconverted energy is converted into heat, which must be dissipated by a water-cooled heat sink. This makes these lasers energy inefficient (leading to higher operating costs due to higher power consumption) and requires a large volume of cooling water. In addition, the doubling crystals degrade over time due to the high power output and, if not carefully managed, can cause reliability problems and downtime for the entire laser.
Another practical problem with green lasers is that the standard optical fibers used to transmit the green laser beam through the light darken more easily, reducing their lifetime. Specialised green light fibres can overcome this problem, but are more expensive and less readily available. The darkening effect also increases with fibre length. This currently limits the length of the fibre to 10 m, which reduces the flexibility of laser placement in a production environment. In addition, commercially available green, high-power, CW lasers are currently limited to 2 kW of maximum power.
Most industrial lasers have output in the near-infrared, so the entire infrastructure to support them is based on this wavelength. For example, the available selection of process heads for green lasers is limited and often needs to be customised. Similarly, auxiliary lenses, protective coverslips and other optical components are mostly designed for infrared lasers. Thus, a manufacturer already using infrared lasers may need to maintain a larger inventory of spare parts and consumables to accommodate the use of green lasers in their operation without service delays and downtime.
COHERENT HighLight™ ARM fiber laser
Fiber lasers are much more energy efficient than solid green lasers. This means they require less electricity to achieve a given output power and produce less waste heat. This reduces operating costs and simplifies laser cooling. In addition, fiber lasers are very reliable. In addition, their infrared output beam is easily distributed by optical fibre. However, despite these desirable features, they have not been widely used for welding copper in particular, due to the problems previously mentioned.
Several years ago, Coherent introduced the HighLight series of adjustable ring mode (ARM) fiber lasers to bring the cost and practical advantages of these sources to applications that were not adequately addressed by traditional technology. Typically, these are tasks where the spatial distribution of power and power density on the working surface must be carefully controlled to achieve good weld quality (low spatter, minimal cracking and reduced porosity). Typical examples are zero-gap welding of galvanised steel, welding of powertrain components without spatter and welding of aluminium suspension parts without cracking and without the use of additional wire.
This precise control over the spatial distribution of power is achieved by the ARM laser's unique output beam, which consists of a central point surrounded by another concentric ring of laser beam. The output at the centre and ring can be independently adjusted and modulated as required, allowing very close control of the melt dynamics.
Coherent HighLight ARM lasers are available with different center-to-ring ratios and different power levels that can be tailored to specific applications. The center diameter can be configured from 22 µm to 100 µm and the outer ring diameter can range from 140 µm to 200 µm.
High intensity and high power of the center beam is required for copper welding. This provides the energy needed to easily melt the material, despite its relatively low absorption coefficient, while the ring beam helps to stabilise the keyhole during welding. As a result, the welding process is initiated and maintained consistently regardless of changes in the workpiece surface, overcoming the limitations encountered with traditional fiber lasers.

Figure 1: HighLight FL4000CSM-ARM fiber laser.
Copper welding results
Coherent's application engineers conducted a series of tests welding copper using the ARM laser with a high brightness 22 µm diameter central beam and a 100 µm/170 µm inner/outer diameter circular beam. The laser was focused using a remote processing head with a magnification of 1.4, with nitrogen as a shielding gas and a cross-jet. The material to be welded was pure copper. The laser power was 4 kW, with 1.5 kW in the centre and 2.5 kW in the ring for all tests.
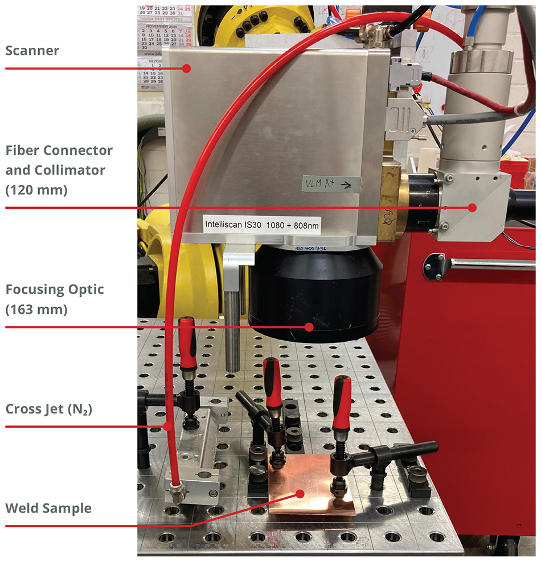
Figure 2: Results of welding copper ARM with a high brightness fiber laser, scanner and shielding nozzle.
The focus position was varied and it was found that the best weld quality was obtained with the focus set 1.5 mm above the surface of the material. Specifically, this position was the best compromise between weld penetration and weld quality. The ARM laser produces deeper weld penetration when focused directly on the material surface, but the resulting weld surface and spatter quality is not sufficient for typical e-mobility applications. The beam profile on the working surface using the optimum beam focus position (1.5 mm above the surface) is shown in the graph.

Figure 3: ARM beam profile on the working surface (1.5 kW center and 2.5 kW ring) with the laser focused 1.5 mm above the working surface.
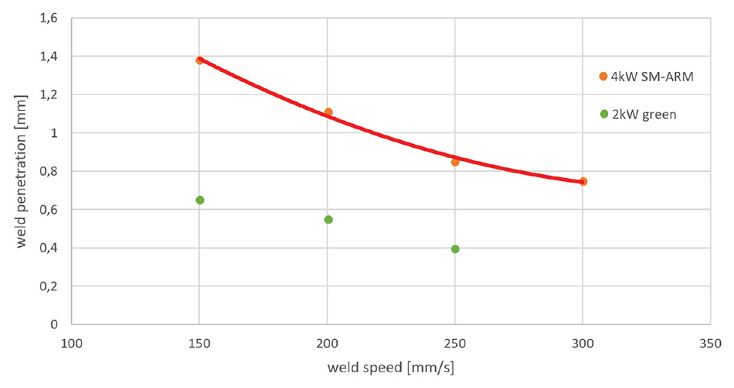
Figure 4: Weld penetration for the 4 kW high brightness ARM laser compared to the 2 kW green fiber laser.
Welding efficiency
The welding efficiency of the ARM laser was also measured and compared to previously published results for the 2 kW green fiber laser. Nitrogen was used as the shielding gas for both welds. The published data for the green laser showed a constant weld cross section of 0.5 mm² and a weld depth of approximately 1 mm. The ARM laser was configured to achieve the same results. Specifically, this required an output power of 3.5 kW and a welding speed of 300 mm/second compared to a welding speed of 200 mm/second for the 2 kW green laser. Normalizing these results gives a linear laser power of 10 J/mm for the ARM laser compared to 11.8 J/mm for the green laser. The green laser therefore offers a slightly higher welding efficiency. However, the higher overall power of the ARM laser allows much higher welding speeds to be operated, despite this small difference in efficiency.
Surface quality
Another important aspect is the surface quality. Traditional fiber lasers are capable of welding copper, but are very sensitive to changes in surface quality. The photo shows an ARM high brightness laser welder on ground and polished copper. The process remains stable on both surfaces with no change in weld quality.
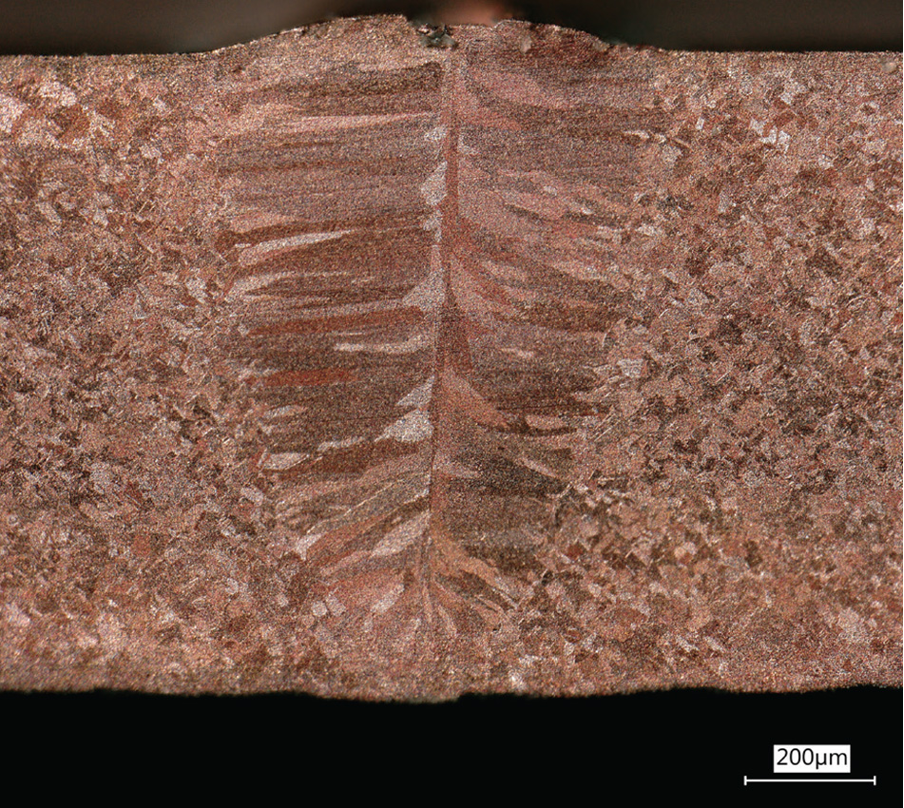
Figure 5: Cross-section of a copper weld formed by a high brightness ARM infrared laser with an output power of 3.5 kW at a welding speed of 300 mm/s.
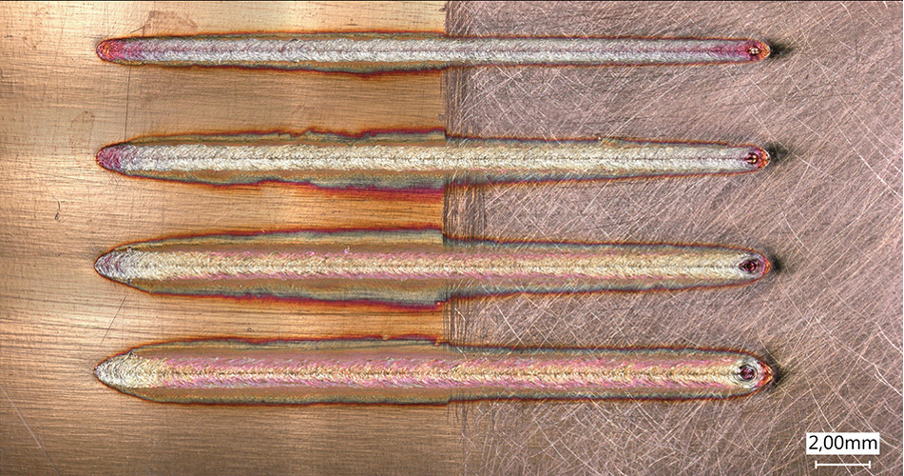
Figure 6: Consistent welds on plain and ground copper using a 4 kW ARM laser at different speeds (300-150 mm/s top to bottom).
Conclusion
These tests have demonstrated that Coherent's high brightness ARM laser is a practical solution for demanding e-mobility copper welding applications. The welding speed and process speed meet or exceed current production requirements. In addition, the ARM laser does away with the problems of surface quality sensitivity and process instability that have limited the use of fiber lasers for copper welding in the past. Thus, the ARM laser finally brings all the cost, reliability and practical advantages that have made fiber lasers the choice for many other industrial applications, even to the demanding task of copper welding.
Source: coherent.com